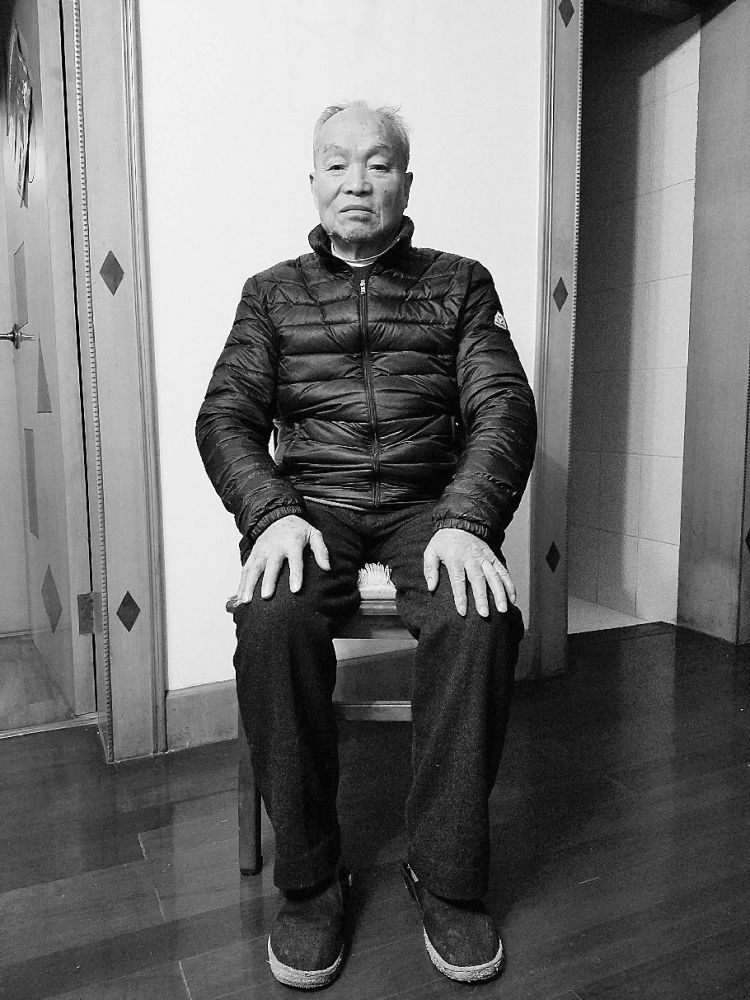
【口述者简介】孙祖安,男,1934年出生,1950年当学徒,1958年进入杭州轴承厂,七级钳工,技师。 我是杭州人,小时候住在回龙庙前57号。父亲是杭州锦丰绸厂的挡车工,母亲是家庭妇女。家里兄弟姐妹5人,我排行第二,上面还有一个姐姐。一家7口人,仅靠父亲每月一石半米的工资过活,所以日子过得比较艰难。 尽管家里条件不好,但父母亲还是尽可能地创造条件让我读书识字。10岁左右,我被送到庆春路的一个叫天真观的道院里读小学。那时候杭州正规的小学很少,很多学校都办在寺庙道观里。我在那里读了2年半,后来因为家里实在支付不起学费而辍学。后来,父亲所在的 锦丰绸厂在王马巷办了一所子弟学校,叫集成小学,我就在那里又读了1年。辍学的原因,依然是没有学费。我至今仍记得学校的校长一大早站在校门口,把拖欠学费的学生一个一个拎到一边,不许进校门。 我那时已经16岁,比旁边同学高出一个头,站在门口感觉很难为情,只能低着头回家了。 一心只想学技术 既然书读不成,我就决定出去工作。那时我家一带有不少织布作坊,我就去作坊里打线(把多股线捻成一股),一天大约能赚1元钱。但小作坊的织布工作受季节影响很大,春夏活比较多,冬天基本就没活干了,收入很不稳定。所以我在做打线工的同时,作为待业青年在居民区登记找工作。1952年登记,一直到1954年才有回音。 1954年初,衢州机场翻修扩建,需要大量劳动力,杭州市劳动局组织适龄待业、失业青年赴衢州“以工代赈”。我从居民区收到了参加机场建设劳动的通知后非常激动。衢州机场是军用机场,去那里工作就是参加国防建设啊!1954年2月,我们近千人组成杭州第四大队出发去衢州。在衢州干了8个月,我做得最多的就是挑泥土。修建跑道、机堡都需要开出大量的土方。我们上万工人就像一只只蚂蚁一样,在初春寒冷的田畈里,依靠肩挑手扛,一点一点把机场建设起来。我还因为出勤率高、工作表现好,获得了个人二等功。回到杭州后,因为在衢州的优秀表现,劳动局安排我到军区后勤部上班,负责接待工作,不过是临时工。 1956年,锦丰绸厂招工,我兴冲冲地就去报名了,很顺利地就进厂了。去军区后勤部辞行的时候,领导还挽留我,说通过1年多的工作,觉得我这个人责任心很强,工作非常勤恳也很用心,从不偷懒耍滑,让我不要去工厂,就留在军区,他已经向军区申请到正式编制给我了。但是我一口就回绝了他,因为我当时一门心思想学技术,在后勤部做接待工作,一点技术含量也没有,而且我文化程度又不高,更需要一门技术傍身。就这样,我进入锦丰绸厂工作,当时给我定的工资是38.5元一个月。 赴哈尔滨学习冲压技术 1958年,国家“大炼钢铁”“大办工厂”,杭州许多大型工厂就在这时建了起来。由国家机械工业部出资建造的杭州轴承厂也开始筹备建设了。当时有个政策是“轻工业支援重工业”,我被厂里选中抽调到轴承厂。6月,我到位于湖滨八弄的杭州轴承厂筹建处报到。因为还在筹建阶段,轴承厂一无厂房(只向在艮山门的杭州市手工业合作社借了一个车间),二无机器设备,三无生产技术。报到的工人无处可去,筹建处就组织工人学习文化知识,分组读报,开会学习机械工业部的文件通知,学了几个月。 1958年10月,厂里决定选送工人到外地轴承厂学习技术。当时全国有三大轴承厂,分别是哈尔滨轴承厂、瓦房店轴承厂和洛阳轴承厂。经国家机械工业部协调,杭州轴承厂的工人安排到哈尔滨轴承厂学习培训。于是我就坐上了去哈尔滨的火车,一同出发的有七八十人,学各个工种,我是学做冲压工。 到哈尔滨后,我们就按工种跟随各自的师傅学习,我跟的是一个冲压工老师傅。冲压工,简单来说就是利用冲床和工装模具,对金属材料落料加工,进行初步定型。冲床操作的时候节奏快、压力大,很容易出安全事故。所以,学习的第一个月,师傅不允许我动手,只能在一旁看。我一边看着师傅操作,一边就把他的各个动作和要注意的地方都牢牢记在心里。第二个月以后,师傅才在下班以后留出15分钟到半个小时,允许我尝试操作冲床。 当时我就对加工技术表现出极大的兴趣,在旁边看师傅操作冲床,手就“痒”得很,一心就想自己操作。另外,我一直研究冲床的操作工艺、机械原理和冲压的流程,有时候甚至觉得某些流程和操作 可以做得更好。我就问师傅,为什么要这样操作,为什么模具要这样安排。很多时候师傅都回答不出,只是告诉我他的师傅就是这样教他的,按照经验做就可以。这样的回答根本满足不了我,所以一有空我就在车间里到处转,观察各个工种操作,还向工具车间的工友请教模具制造等。 1959年1月,通过3个月的学习,我基本掌握了冲床的操作技巧和各个注意事项,就跟随大部队按照计划返回杭州。那时轴承厂的新厂房在石桥地区建设得如火如荼,我们培训回来后就加入到基建工作中。一直到1959年的下半年,轴承厂崭新的厂房矗立起来了,机器设备也陆续到位,各项生产工作慢慢走上正轨。 练就模具修理技术 在轴承厂,我所在的车间叫钢球车间,轴承一共5个部件——内圈、外圈、保持器、钢球、铆钉,其中保持器、钢球、铆钉这3个部件是由钢球车间生产的。车间里有20多个冲压工,实行三班制,机器24 小时不停。 制作不同的零件,冲床冲头的高度和模具安装的位置是不一样的,冲头越低产生的压力越大,越高就越小。压力过大,产品就变形了,压力太小,冲压不到位,所以冲压工需要经常调整这些位置。许多冲压工只会操作冲床,不会做调整,所以车间里专门设置了调整工,来干这个活。我去哈尔滨学习培训过,虽然时间不长,但在车间里已经算是“老师傅”了。所以做了没几个月车间里就把我安排为调整工了。调整工属于钳工,和冲压工是两个工种。那个时候国家实行计划经济,买东西都要凭票。普通居民一个月是24斤粮票,冲压工是30斤,钳工是35斤,锻工是40斤。我做调整工后,每月的粮票涨了5 斤。 在冲压过程中,冲压模具因为经常受到冲头的挤压而损坏。对损坏的模具,当时大家的普遍做法就是更换一副,换下来的模具有些返还工具车间修理,有些就直接报废了。报废一副,成本很高。返回修理,工具车间连制作新模具都来不及,更不要说修理了,有时候冲床还会因为模具不能及时供应而停止工作。所以,如果能及时快速地修理这些模具,不但能降低生产成本,还能提高生产效率。 保持器的生产环节,主要有切料、成型、整型、冲孔4道工序。经过我仔细观察,发现每一道工序可能造成的模具损坏都不一样。比如切料模具容易磨损,只需要稍作整形就可以继续使用。成型模具是用来压制形状的,压得多了,自身也会有一定程度变形,轻度的变形可以用金刚石磨回来,大的变形就先退火(降低金属硬度),然后用锉刀重新造型和再进行蘸火(蘸火可增加金属硬度),很多模具只要修理就可以重复使用了。慢慢地,我在本职工作之余,开始做一些模具修理。 随着我修理的模具越来越多,我修理的技术也越来越高、速度越来越快。钢球车间的生产成本有了大幅度的降低,节省了大量钢材(模具大多是钢制的),生产效率也有提高。车间和厂里的领导都非常高兴,把我的工作重心转移到模具修理上了。当时轴承厂只有我一个人干这个工作,要修理的模具很多,所以经常是加班加点地做。因为修理模具为厂里节省了成本,厂里推荐我作为1961年的先进生产工作者代表,参加全市的表彰大会。 成功打磨战斗机轴承钢球 1963年,我开始任钢球车间主任。我前面说过,我对技术非常热衷,所以我虽然做了车间主任,但是不脱产的,我除了参加厂里的会议外,其他时间都在一线做的。不但不脱产,做了车间主任后,我对自己技术方面的要求反而更高了,除了钳工技术,我对车工、磨工等工种的操作技能也掌握了很多。所以说,我的工作衣从来没脱下过。 20世纪70年代后期,厂里来了2个笕桥机场的技术员,他们带来了战斗机上轴承使用的10组钢球。经过鉴定,这批钢球表面有缺陷,达不到光洁度要求,短时间内采购不到货,任务又非常紧急,就到轴承厂来寻求帮助。负责处理这件事情的是厂里的技术科,技术科的同志 一看是钢球的问题,就到了我所在的钢球车间。 钢球的制造工序主要有冲压(定型)、车削、软磨、硬磨(蘸火后)、精磨、超精磨6道工序,制造完成的钢球对光洁度有很高的要求。我仔细看了他们带来的钢球,了解了工艺要求。对这些钢球再次进行打磨提高光洁度,是没有问题的,但是再次打磨的钢球肯定会缩小尺寸。所以我又谨慎地向他们询问了尺寸的要求和工作的时间要求,他们表示在尺寸方面,只需要各组内部的20颗钢球保持一致就可以,相互之间没有严格要求,时间上只是尽量抓紧。 他们的回答让我松了一口气,但毕竟是飞机上用的零件,200颗钢球,一颗出错,导致轴承出现问题,那后果可能就是毁掉一架飞机。这样责任重大、技术要求又高的活,我决定自己上手来做。我磨的时候,技术员按照部队的纪律,人不离开零件,一直盯在旁边看。我花了两天时间,把200颗钢球全部磨好。磨好后,他们拿出自带的航空汽油,现场清洗钢球,清洗后的钢球在阳光下闪闪发亮,拿到显微镜下检验,光洁度完全符合标准,他们非常满意。 1984年,因为工作需要,我离开了钢球车间,到机修车间做划线钳工。从车间主任回到一线做一名普通工人,现在看来可能会有点不可思议,但是当时我一点思想负担也没有,因为都是工作需要:机修车间缺少一名高技术的钳工,而我又对一线工作充满热情,所以就过去了。做了4年划线钳工,1988年厂里安排我到机修分厂任副厂长,后来又到保持器分厂任副厂长,一直到1994年退休。 |